Sign up here to subscribe to the Grower2grower Ezine. Every two weeks you will receive new articles, specific to the protected cropping industry, informing you of industry news and events straight to your inbox.
Jun 2020
Heat Pump Technology

Energy solutions are here but case study required
Increased ETS (Emission Trading Scheme) charges are going to severely hinder the ability for greenhouses, that use coal fired burners, to potentially stay in business in New Zealand. Gas prices will keep increasing, and securing long term contracts is already becoming difficult. This has forced growers to start investigating possible alternative energy solutions.
The good news is I believe that currently there is technology available, the bad news is neither industry or government (to my knowledge) have conducted detailed case studies on alternate energy sources for the greenhouse industry. We know that one large company in NZ uses geothermal energy and another waste methane from a green waste landfill. Traditional ways to heat greenhouses in NZ is to use Natural Gas, Coal, Waste Oil. Biofuels or waste material may be an option but the logistics, including storage requirements and lots of large trucks transporting woodchip, is expensive and complicated. Not to mention the diesel required for those trucks.
Luckily, I have been able to visit many greenhouses in the UK, Holland, Belgium, Portugal and Australia over the past 15 years. During a family holiday in 2017 I could not resist the opportunity to visit a 4ha tomato grower, near Hull in England, where I was staying for a few days. Chris Durnford, owner of Red Roofs Nursery Ltd, kindly gave me a few hours of his time. As part of Chris’s heating system, the company uses ‘heat pump’ technology to convert 11-degree centigrade water up to a maximum of 55-degree centigrade. As a result of the energy issues our South Island growers are facing, I recently e-mailed Chris to ask a bit more in regards to how the heat pump technology works:
We have an open loop system where we pull up 80m3 per hour of water at 11-degree C. The heat pump takes the heat down to 5c which is then returned to the ground via another borehole.
The heat pump will produce heat up to 55c but we tend to run between 35c and 45-degree C. The lower the temperature the more efficient the system. I find that with good quality thermal screens, this gives plenty of heat to the tomato crop.
We are actually in the process of redeveloping our old nursery and are putting in exactly the same system but this time to heat the whole site. Pure CO2 will then be use to provide the plants CO2 requirements.
My main piece of advice is you must get the water quality correct to prevent pollution in the heat pump.
Red Roofs Nursery heat pump system was designed and installed by European company Certhon. Certhon designs and realizes renewed and reliable techniques which make the cultivation of horticultural products worldwide enable.
Heat pumps are an ingenious system for heating and cooling greenhouses in an energy-efficient way. Certhon has developed heat pump solutions around the world based on the same underlying principle: extracting low-quality heat or cold from the environment and then redirecting and processing the heat to a higher temperature, after which it can be used elsewhere. The amount of energy needed to power the heat pump is lower than the output.
For many greenhouse horticulture companies, the water pump is a profitable alternative to traditional heating and cooling techniques. Certhon can arrange the entire process from A to Z: from initial capacity limitations to digging the wells.
Source – Certhon. www.certhon.com
https://www.certhon.com/en/news/20150331-red-roofs-nursery-goes-for-perfect-climate
https://www.certhon.com/en/one-stop-shop/heating-cooling
https://www.certhon.com/en/greenhouse-solutions/innovations/energy-saving-greenhouse
Christchurch Airport:
The story does not end there. In 2011 Christchurch airport had installed a heat pump system that uses 12-degree ground water to predominately cool and heat the airport.
The systems clever design means that very little energy is wasted. When ambient temperature permits, water from the wells is used to cool the airport from chillers. The 12 degree C water is pumped from the aquifer via boreholes to heat exchangers. This cools the water in the loops which travel around the airport.
To take advantage of the efficiencies of the ground water cooling, spaces that require year-round cooling hare air-conditioning systems designed to operate solely on ground water.
In addition, the chillers work in combination with the ground water. When direct cooling is not covering demand, the water can be further cooled by the chillers.
Areas subject to seasonal changes are designed to utilise a combination of ground water and mechanical refrigeration cooling. When the temperature cannot be achieved using ground water alone, mechanical refrigeration is enabled in stages to match the demand from the building.
Most of the HEATING requirements at the airport are also fulfilled by the chillers. By acting in reverse (as geothermal heat pumps) the chillers remove heat energy from the ground water. This energy is used to heat the 40 degree C heating loop. The ground water is then returned to the aquifer several degrees colder.
Case Study:
The fact that this technology is not only available worldwide but is implemented in NZ demonstrates this has to be an option to be looked into. Scale is important, as many greenhouses using coal as their primary energy source are smaller than 1 ha with the exception of several larger properties. Understanding the costs for different scales of operations is crucial for determining Return on Investment. Could this be achieved? Without knowing, having hard data, how can we consider this possibility?
Photo above of waste oil storage tank, and below a boiler operating on natural gas.
I appreciate your comments. Please feel free to comment on the grower2grower Facebook page:
https://www.facebook.com/StefanGrower2grower/
Article Written and compiled by Stefan Vogrincic, Consultant, Grower2Grower
Article Edited by Marie Vogrincic, Editor, Grower2Grower
CLASSIFIED
Subscribe to our E-Zine
More
From This Category
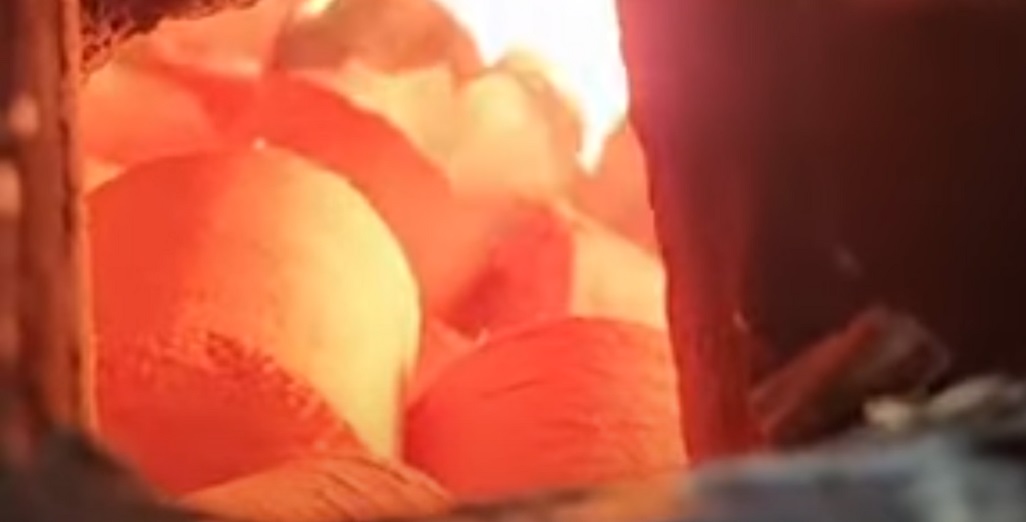
2024 – The NZ greenhouse energy sector Grower2Grower report
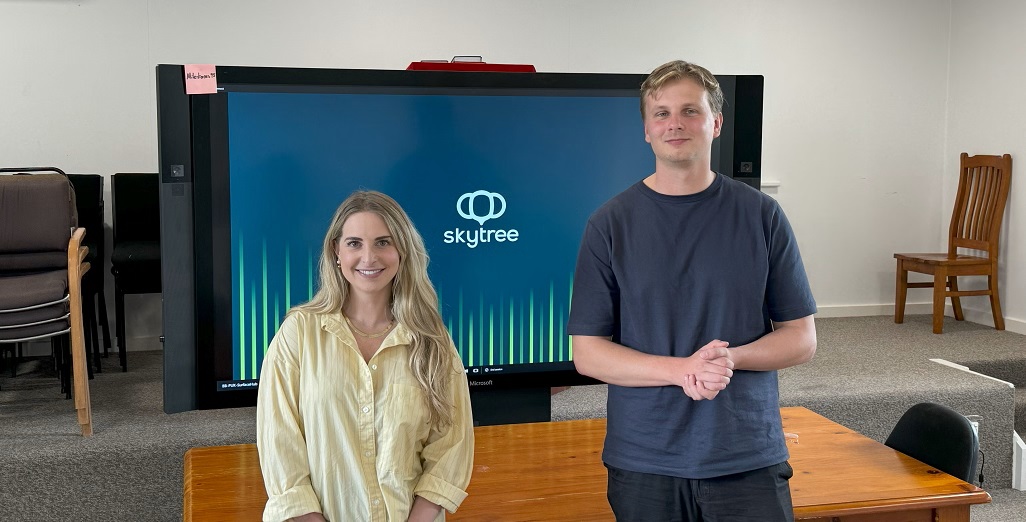
Direct Air Capture (DAC) is now a reality— Onsite CO2 generation scalable for both large and small operations
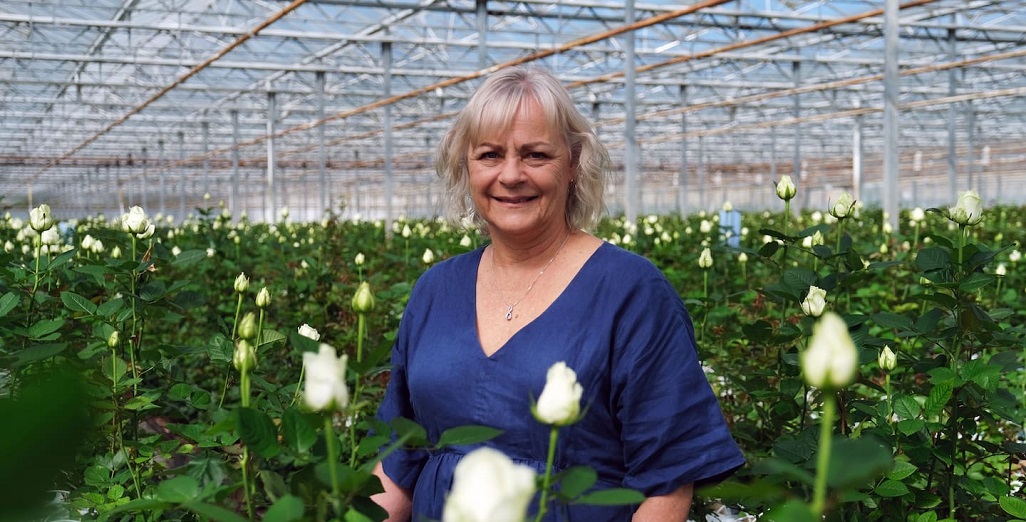
Auckland plant nursery goes electric in pilot scheme
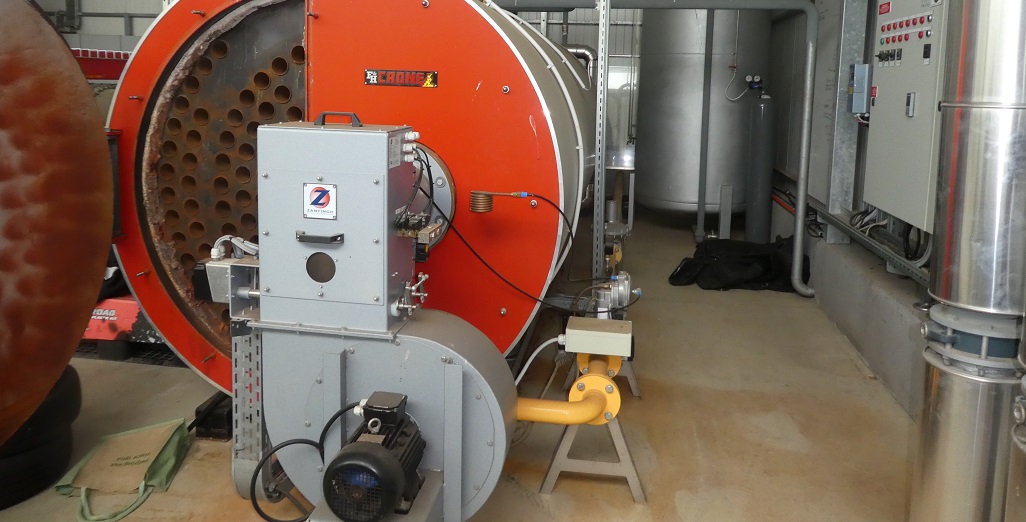
Gas supply for households and small business
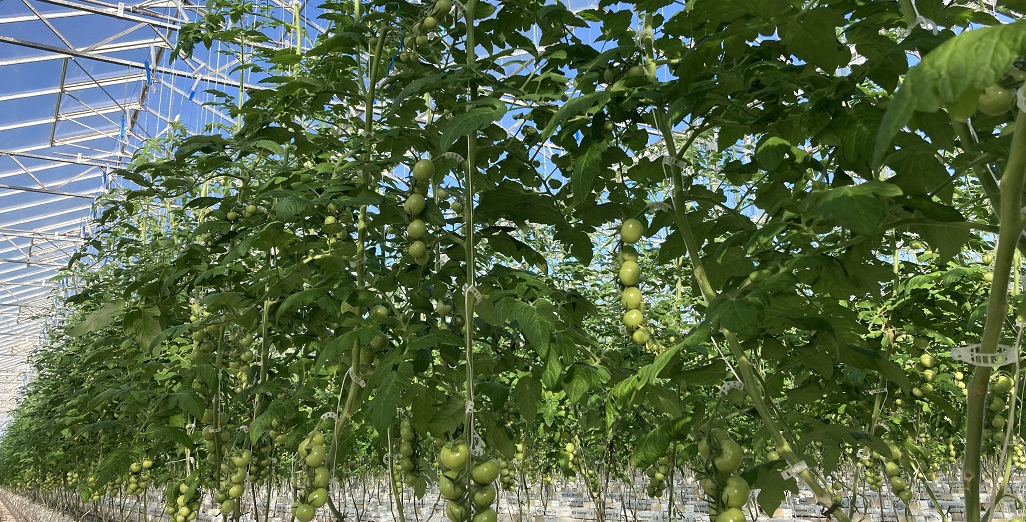
Geoheat Potential of the Tauranga Geothermal System
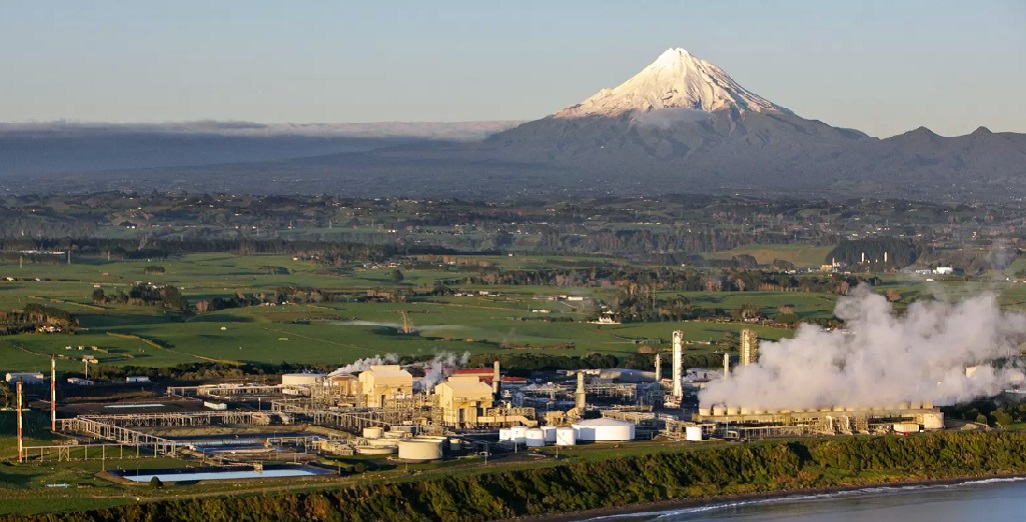