BANANAS by Mike Nichols
I recently spent a few days in Northland visiting tropical fruit growers. Bananas have been grown in the top half of the North Island for many years, but mainly as the occasional plant situated in a sheltered site or close to a north facing wall. Bananas are a tropical fruit and require warm conditions if they are to thrive. For this reason, almost all of the bananas consumed in New Zealand are imported from tropical countries (mainly Philippines and Ecuador), where labour is cheap, and the climate is suitable. Our neighbour (Australia) grows their own bananas (mainly at Coffs Harbour and in North Queensland), and overcome the problem of a high wages country by prohibiting imports. Thus, the retail price of bananas in New Zealand tends to be about half of the Australian domestic price. In Turkey there is a rapidly increasing banana growing industry (8,000 ha) using plastic clad greenhouses near Mersin, which has a similar latitude to Northland, but this is protected by a 100% tariff on imported bananas. The Spanish Canary Islands (which I visited in 2019) exports only to continental Spain, which (although part of EU) restricts the cheaper central American grown bananas into Spain.
So, what future does banana production have in New Zealand? I consider that the prospects are good, provided that we prevent any of the serious banana diseases (such as Panama disease) from entering the country, by ensuring that our plant quarantine is effective in preventing any plant material (except for fruit) from entering the country. ie no unofficially bringing in banana suckers from the Pacific islands. The only fresh plant material must be in tissue culture, and then placed into biosecurity until confirmed as free from any pathogens (current and future).
The second requirement is to determine how best to grow the crop under New Zealand conditions. New Zealand is not the humid tropics—anything but, however this does not mean that it will not be economic and profitable to produce tropical fruits in a sub tropical part of the country. We need to develop our own unique production systems.
In fact a study of the literature demonstrates just how little we know about how bananas grow, and the factors which influence productivity. Because bananas grow so easily in the tropics, the research about them is very limited. When we then try to interpret this into a sub-tropical environment it becomes even more difficult.
Bananas are an interesting crop in that they are propagated vegetatively, either by taking suckers (with a few roots attached) from the base of existing plants, or by tissue culture (which is now the more favoured method). They are best described as day neutral plants in terms of flowering—ie day length does not influence when they flower, unlike short day plants like chrysanthemums or hops which only flower when the day length falls below 12 hours, or long day plants like onions, which only form bulbs under long days. This does not, however mean that they flower after a certain time, as temperature and other climatic factors will also influence flowering time. At the base of the banana plant is a corm like structure from which shoots develop, and one of these will become the main shoot. All the leaves and the flowers are developed at the base of this shoot, and grow up within the pseudo stem—which is really the base of the earlier leaves. Depending on temperature the banana produces about 1 leaf every month, and flowers after it has about 40 leaves, however at any one time it probably only has some 8-10 leaves, as the older leaves die and are damaged by the wind.
It appears that floral initiation may well be critical in New Zealand as the majority of fruit I have seen tends to be short, and the bunches may require thinning to increase fruit size. Temperature during the flower initiation phase appears (from the literature) to be critical. As the majority of New Zealand production appears to have been outdoors, this may well sort itself out due to global warming and protective cropping—only time will tell.
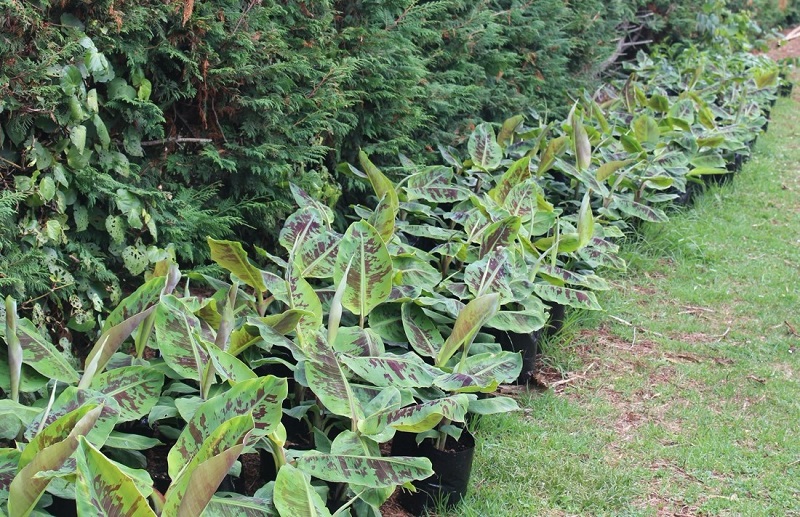
Fig1. Young tissue cultured banana plants.
Of course, there are a number of questions which must be asked about the quality of the locally produced banana. Certainly, in my “limited” experience they have a nicer flavour and texture than the imported bananas, and they have thinner skins. Obviously, they will be higher priced than imported produce–NZ labour is a little more expensive than in the Philippines and Ecuador. Harvesting, however is not time demanding, as this simply involves cutting the stem of the banana plant half through close to the ground and lowering it down until the bunch of bananas can be easily removed from the plant. ie as much as 20-40 kg or even 60 kg of fruit harvested at a single time!!!
Obviously, productivity will be the key to whether a successful local industry can be developed. Certainly, the way bananas are produced in the tropics is not the model to use, and we should be making use of all the best research available. We now know that bananas respond best to warm (optimum 28C), but not hot temperatures—anything over 35C is not good news for bananas. We know that potassium and boron are very important fertilizers for bananas, and that silicon may also play an important role. Regular irrigation is essential, and that a well drained soil is vastly superior to a clay soil.
For New Zealand’s sub-optimal conditions there can be little doubt that some form of protective cultivation is essential, not only to reduce wind damage of the leaves, but also to increase (if only slightly) the ambient temperature.
While in Northland I spent some time at Geoff Mansell’s property near Maungatapere. Geoff is the Chairperson of BONZA, the Banana of New Zealand Aotearoa, and took me to visit several growers in the Whangarei area. Geoff has a property with a soon to be completed large (and tall) greenhouse in which he plans to grow bananas. He also has an outside planting, which is well sheltered from the wind. He took me to visit Linda and Owen Schafli’s property near the Whangarei Heads. Shelter is the key, and they plant their tropical fruit crops in the gullies and leave the ridges in native bush. Not only bananas but pineapples, coffee etc.
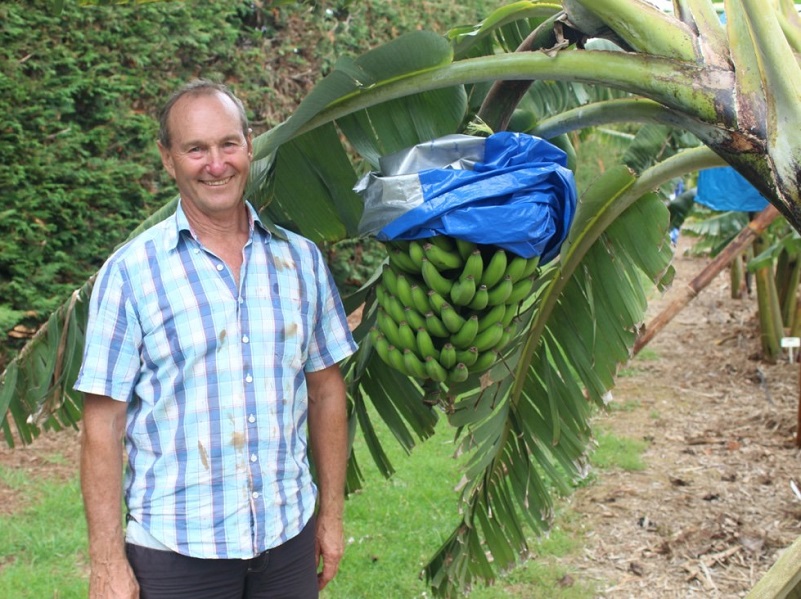
Fig 2. Geoff Mansell shows a typical fruiting banana.
Later that day we paid a visit to Ross and Karen Potter (Sunrise Bananas NZ), who are probably the largest banana growers by area in New Zealand. They are converting a dairy farm into a banana plantation. Still in the early stages, the importance of wind protection for bananas was clearly obvious from the damaged leaves. Natural windbreaks are planted but need a year or two more to really become effective.
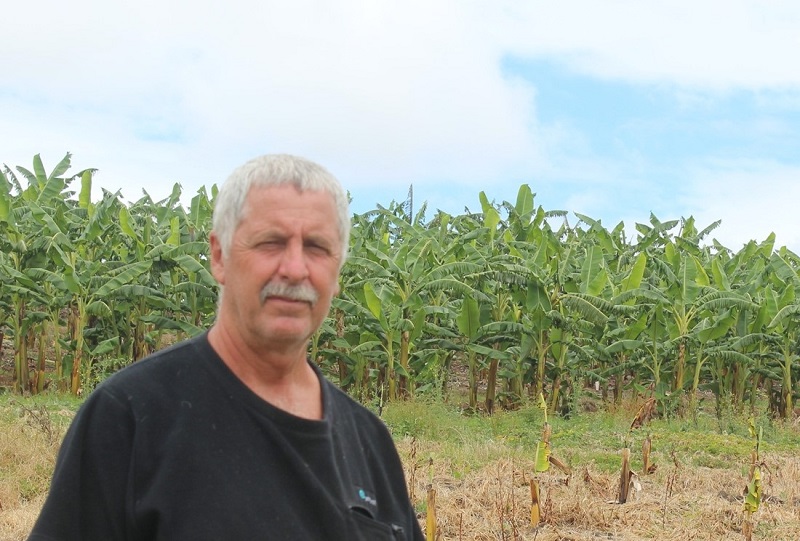
Fig 3. Ross Potter with some of his banana plantation.
Of course, bananas are not only useful for their fruit, as the large leaves can make a very valuable natural (and biodegradable) wrapping for produce (see photo).
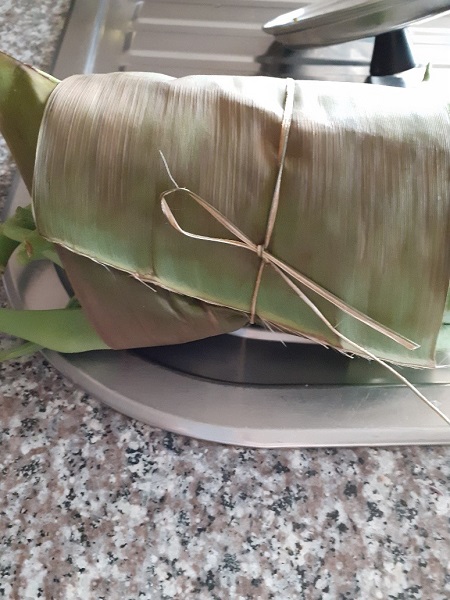
Fig 4. Banana leaves ca be used for wrapping produce
Local banana production is not restricted just to Northland, and I am well aware of the Gisborne group, of an interest in Hawkes Bay, and of the planting by Mathew Bergesen near Tauranga of some 150 plants in greenhouses. The protection from the wind, and additional warmth from the greenhouse shows clearly the large undamaged leaves in Fig 5. There is no reason why greenhouse production should not be considered in any sheltered area north of Taranaki and Hawkes Bay, and even some of the very sheltered valleys near Nelson might be suitable.
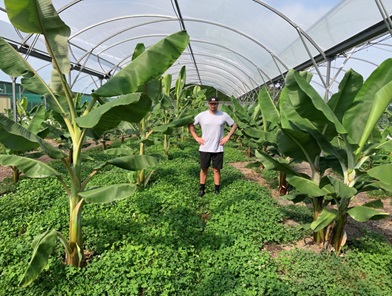
Pic 5. Greenhouse bananas at Mathew Bergerson’s property, Te Puna. Note: excellent undamaged foliage.
A major supporter for local growing has been Dr Jane Mullaney of AgResearch, who has emphasised the potential of tissues culture propagation, and the importance of ensuring that varieties are true to type, by DNA testing.
Marketing is the key to developing a sustainable industry, and for bananas there are two choices. Currently the majority of bananas grown locally are sold through the local farmers markets, but this can only operate close to the production area. The alternative is to use the supermarkets, and this will require strict adherence to GAP.
It is not easy to predict how bananas might develop in Aotearoa in the future, but two factors are clear.
1. Virtually all the crops grown commercially in New Zealand in greenhouses use hydroponics in order to ensure that the plants have an adequate supply of water, nutrients and oxygen (aeration).
2. Clearly if the flower initiation period is the most critical phase in fruit production, and temperature is the determining factor, then research is required to understand the response, and how best to produce high quality bananas consistently in a less than perfect environment.
For further information on BONZA,
contact geoff@bonza.net.nz or david@bonza.net.nz