Sensors that continuously monitor Water Content and EC
This week I came across athe article below on my LinkedIn page. Whether you use Cultilene products or not or use the plant empowerment principals this article explains very precise applications. The paragraph headed ‘Support for decision-making’ looks at the large improvements that have been achieved using sensors to continuously monitor water content and EC in the substrates. In my view this is key for improving overall growing outcomes.
Prioritizing humidity- is another very important factor for New Zealand growers. The negative effects from the lack of humidity control effects all.
Well worth a read and I look forward to your comments. Please e-mail stefan@grower2grower.co.nz or send a message via our facebook page https://www.facebook.com/StefanGrower2grower/
Den Berg Délice group
Since first introducing the Plant Empowerment principles around 18 months ago, Belgian tomato producer Den Berk Délice has made several changes and is already experiencing numerous benefits. Grower Lucas Aertsen explains more in this interview.
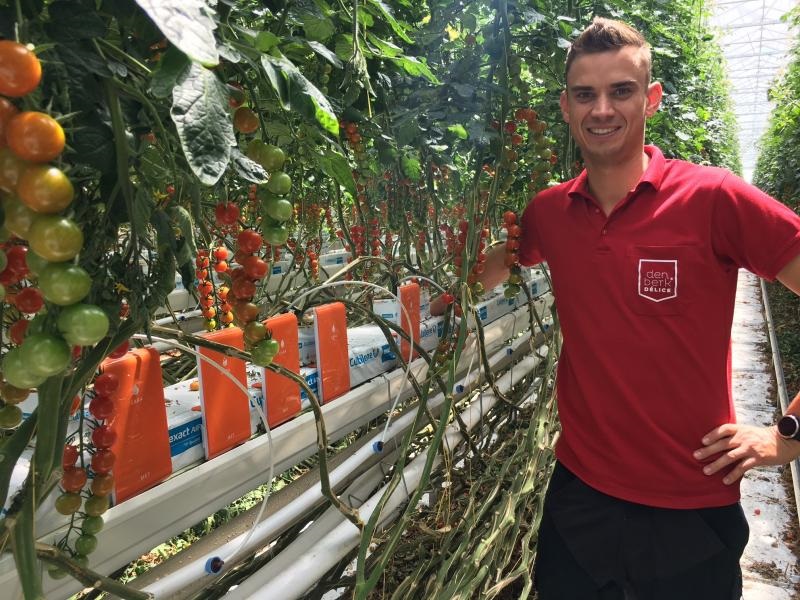
“Plant Empowerment will help us to generate optimal growth with every square metre”
Lucas AertsenSalmmeir – Den Berg Délice group
Lucas Aertsen is head grower at the 9.6ha tomato production facility of Salmmeir BV in the Belgian town of Rijkevorsel. This company – part of the Den Berk Délice group which has a total of 60ha of production across six locations – has a strong reputation for supplying high-quality and flavoursome specialty tomatoes to major retailers throughout Europe. Its main varieties are the red cherry tomatoes Axiany and Sweetelle, plus a number of others for the production of colour mixes.
Lucas has been working in the greenhouse sector since graduating with a degree in bioengineering from Leuven University around five years ago. “What I love about my role is that it’s so broad,” comments Lucas. “In addition to plant biology, I’m involved in new technology and IT, the energy market and, in view of our expansion plans, even construction.” A brand-new 7.2ha greenhouse is currently being constructed, where the first crops will be planted in late August. Besides that, another 8.5ha facility is being added at the end of this year with production scheduled to start in March/April 2022.
Transforming expertise into data
“Our company is expanding so fast that we really need to be data-driven. A couple of years ago we had six or seven growers, but there are now around ten of us and next year there will be 15. Most of the new recruits are relatively young and less experienced. So we asked ourselves how we could transform the expertise of our more experienced growers into data to help the new growers get up to speed quickly,” explains Lucas. In this context, Den Berk Délice installed the LetsGrow.com data platform around 18 months ago and has been working in line with the Plant Empowerment concept ever since.
The ‘Growing by Plant Empowerment’ cultivation method has evolved from the principles of Het Nieuwe Telen (‘Next Generation Growing’), which have been tested and proved around the world ever since first being developed in the Netherlands by P.A.M Geelen, J.O. Voogt and P.A.M. van Weel in 2005. In 2018, the founders wrote a book called ‘Growing by Plant Empowerment’ to explain this integrated approach. It is based on physics and plant physiology and focuses on keeping all the plant balances in equilibrium. Data is continuously collected and analysed during the cultivation process to monitor how the greenhouse conditions are affecting crop performance as the basis for decision-making. The concept is actively supported by a multidisciplinary team of six official Plant Empowerment Implementation Partners, including substrate specialist Saint-Gobain Cultilene, the LetsGrow.com data platform, climate computer provider Hoogendoorn Growth Management and screening specialist Ludvig Svensson.
Better comparisons
“Before the LetsGrow.com data platform was installed, we used to have a weekly meeting of all the growers from all the different companies in the group so we could discuss the results from our crops and varieties together. This entailed a lot of Excel sheets and printouts from the climate computer, and the preparation was very time-consuming. Nowadays, the previous day’s climate data is automatically sent to each manager via LetsGrow.com and we receive an overview once a week, plus we can always use our own dashboard at any time. This makes it much easier to access reliable data as the basis for comparing and discussing crop performance,” he adds.
To help Den Berk Délice get the most out of the Plant Empowerment principles, the company has been receiving training since October 2020. “All our growers attend a two-hour online session once every two weeks. The theory from the various chapters in the book forms the basis, but the course is also tailored to our own real-life situation,” comments Lucas. “We use our own dashboard and explore the balances, such as water, energy, assimilates, the influence of the screening strategy and so on, based on topical issues. The course is presented by experts from LetsGrow.com and Hoogendoorn Growth Management with input from the other Plant Empowerment implementation partners behind the scenes.”
Sharing knowledge
“We don’t want to be an inward-looking company – we believe it’s important to stay in touch with the market to hear about the latest developments, share knowledge and gain new insights that will help us to continuously improve. And our contact with the Plant Empowerment implementation partners plays a key role in that,” he continues.
Above all, Lucas has noticed that working in line with the Plant Empowerment principles has shifted the focus from subjective intuition to objective data. “That creates some lively discussions!” he says. “We have a very experienced grower on our team who has been in the tomato business for more than 20 years. We see it as a challenge to convince him to let us try things out based on the data insights, and it’s satisfying to see him gaining confidence in the data when he sees that it actually works.”
Support for decision-making
The rootzone is one area in which those data insights have made a big difference. In spring 2020, Den Berk Délice worked with Saint-Gobain Cultilene to install CARA MET sensors which continuously monitor the water content, temperature and EC in the substrate and communicate wirelessly via the cloud. All the data is displayed in the Saint-Gobain Cultilene dashboard on the LetsGrow.com platform. “This really supports our decision-making. Flavour is very important for us; we aim for a brix of 10.5 in our tomatoes to achieve the desired sweetness. The brix value is mainly influenced by the EC in the substrate, so if the brix drops below 10 that’s the first thing we look at – and we now have that data constantly at our fingertips.”
All the data has revealed some interesting interactions, according to Lucas: “For example, we can monitor both the EC and the radiation level changing throughout the day to identify when it’s the best time to reduce the EC. And last year, the data enabled us to experiment with the EC reduction in combination with both our irrigation and ventilation strategy. In the right combination, the plants stayed active for longer and were much better balanced in terms of photosynthesis and keeping themselves cool, with no plant stress.”
Prioritizing humidity
Another change resulting from the Plant Empowerment approach has been a better understanding of the role of humidity and screening. “In the past we were focused mainly on the temperature in the greenhouse, but thanks to the data insights, we’re increasingly using humidity to create an active climate – particularly in the spring and summer – by balancing our ventilation, lighting and heating strategies in line with the outdoor conditions,” says Lucas. “And our screen supplier Ludvig Svensson, another Plant Empowerment implementation partner, helped us to develop a screening strategy to maintain the optimal temperature, not only in the greenhouse but also in the plants themselves. On cold days, we now use screening more intensively to prevent energy loss from the top of the plants; it’s important to keep them warm to stimulate active growth. However, we always leave the screens around 15-20% open to allow the moisture to escape. So overall, we’re much more focused on achieving the right moisture balance – both in terms of what the plants receive and what they produce.”
The new greenhouse currently being built at the Salmmeir facility will be fitted with a hybrid top-lighting system including LEDs at 265 mmol rather than the 180mmol currently used. “Now that we have even better control over the climate and can maintain a better plant balance thanks to the Plant Empowerment approach, we believe we can work with higher light intensities and for longer periods. Some varieties will perform better under more light than others, of course, so it will still be a matter of combining the data with our own insights and experimenting with things like plant spacings. But the data gives us an excellent basis to start from.”
Sustainability
Last but not least, sustainability is important for Den Berk Délice. For example, the company is continuously working to further enhance its closed-loop water system, plus it is building a new storage and sorting facility which will be equipped with solar panels and be directly connected to a local industrial park’s network for thermal energy recovery. “Growing in line with the Plant Empowerment principles also supports a sustainable approach,” states Lucas. “As the agrifood industry continues to scale up, data will enable growers to manage ever-larger crop production areas. Plus by sharing knowledge, gaining new insights and optimizing our use of the very latest technologies, we can generate a better yield from every square metre with the optimum use of resources – and that’s what I personally find most important,” he concludes.
Source – https://www.plantempowerment.com/user-story/den-berk-delice/
This article was republished with the permission of Remy Maat, consultant at Saint-Gobain Cultilene.