Sign up here to subscribe to the Grower2grower Ezine. Every two weeks you will receive new articles, specific to the protected cropping industry, informing you of industry news and events straight to your inbox.
Aug 2020
Berry set ups in high and low tech Greenhouses
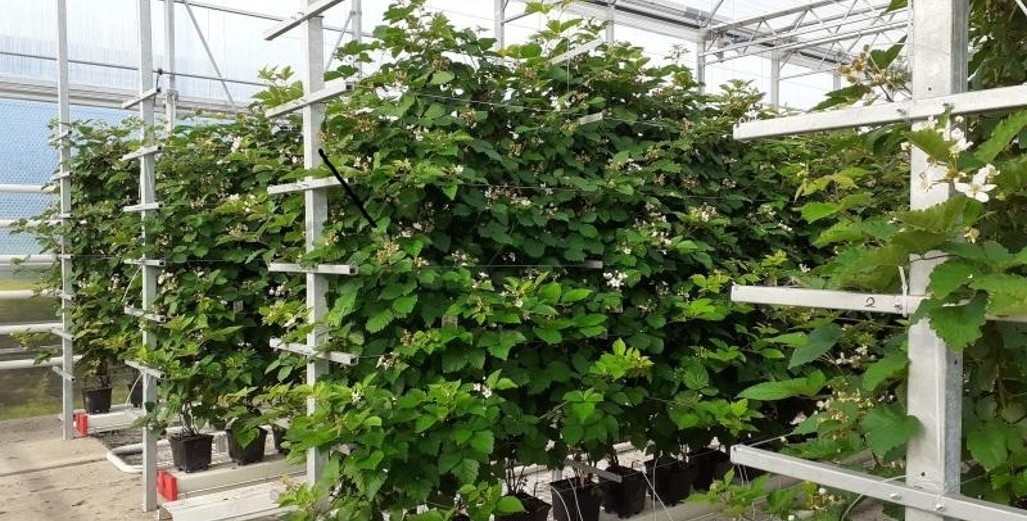
Companies Decisions based on ROI
As the berry season rolls around many traditional outdoor berry growers have ventured into protected cropping. Investment growing berry’s using high-tech facilities is not currently an option for New Zealand growers. The production and efficiency benefits, between low and high-tech growing, must be negligible for any company to justify the capital spend on high-tech.
In the photos posted below I have made some observations. These are just my personal observations but think they will be food for thought.
In this photo from overseas, you will notice the picture-perfect uniformity of the operation.
- Grow gutters
- Heating pipes/transport system
- Pressure compensating drippers
- Strong and sturdy trellis system to hold the horizontal crop wires
The gaps, in between rows, are a little bit hard to estimate but I would say they are roughly 2 metres apart, similar to some cucumber properties row spacing. The plants are left to grow higher increasing the opportunity for more production. Picking from scissor lift trolleys will make picking efficient. It is interesting to the see the bucket spacing and therefore the canes per pot. Some systems have larger bags with five or so canes per pot/bag. In other systems with smaller bags/volume of substrate I have seen two or three canes.
The other add-ons for this greenhouse may be to have supplementary lighting and screens.
This photo is of a similar high-tech raspberry growing operation. It is harder to see but the spacing of the pots/bags on the gutter seem further apart so possibly more canes per pot/bag in this particular scenario.
This is a lovely looking Venlo greenhouse and the big difference between this and the first image is the pipe rail system.
This photo of a poly-tunnel house shows a beautiful crop of blackberries, what is noticeable is the shorter nature of the plants, possibly restricted by the height of the tunnel. There is probably no pipe rail system so harvesting will be more difficult.
In this photo, at a property I visited last year, there were between two and three canes per pot. You will also notice the width of the path. This spacing is based on the requirement to drive a small vehicle down each row. Alternatively, pipe rail systems would give you an opportunity to grow at a row spacing possibly better for a berry plant and also automate picking and spraying.
This image, from the same property as above, illustrates the height of the plant in its mature state, hence why I also think the row spacing is excessively big.
Return on Investment is key to deciding the structure and internal layout for your growing situation. Efficiencies and the cost of labour may be a factor influencing layouts in future years. For now, it is hard to justify high-tech investment. However, it doesn’t mean it would not pay off in the long term, especially if you could grow at any time of the year and there is strong demand from your local market. Exporting opportunities for fresh berries, via air transport, is a strong possibility but will be influenced by current Covid-19 disruptions.
I appreciate your comments. Please feel free to comment on the grower2grower Facebook page:
https://www.facebook.com/StefanGrower2grower/
Article Written and compiled by Stefan Vogrincic, Consultant, Grower2Grower
Article Edited by Marie Vogrincic, Editor, Grower2Grower
CLASSIFIED
Subscribe to our E-Zine
More
From This Category
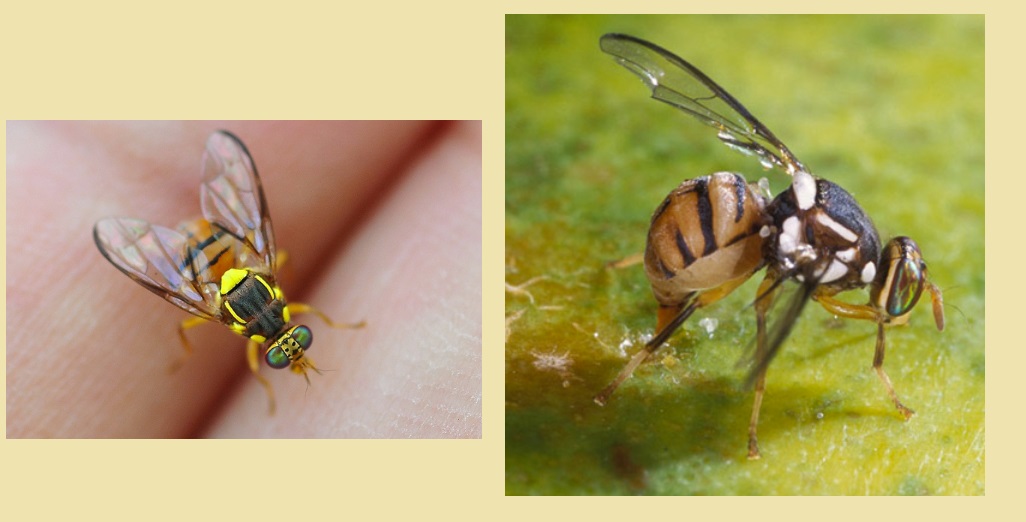
Oriental fruit fly found in Papatoetoe: response underway
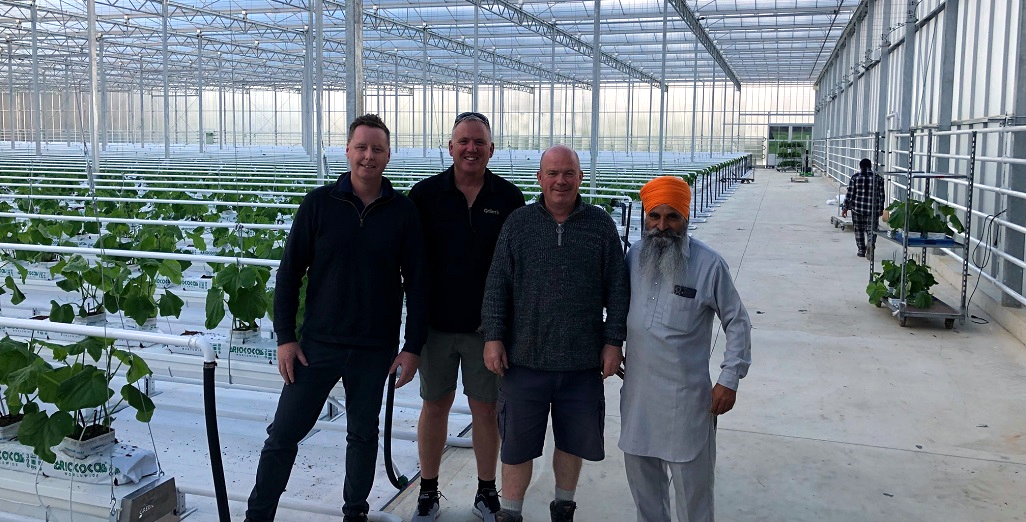
(Best of 2024) Aka Aka Produce celebrate planting in their brand-new high-tech greenhouse
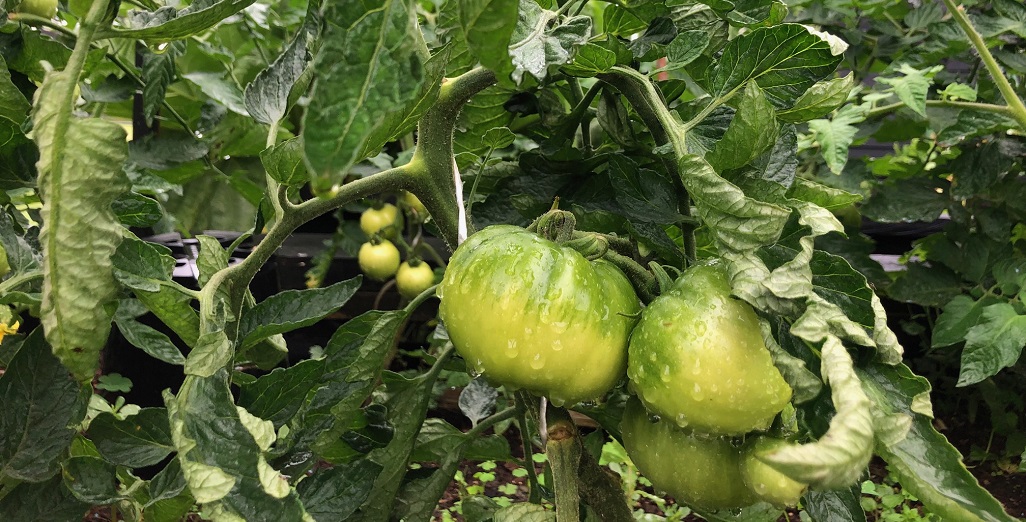
Greenhouse Production in the Future – Mike Nichols
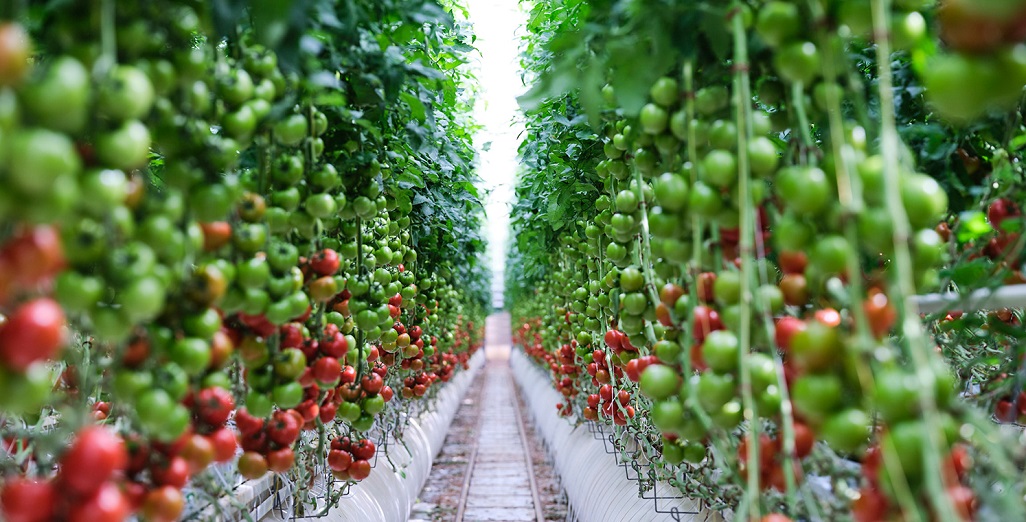
Industry spearheads adoption of labour-saving tech with $52M boost (Australia)
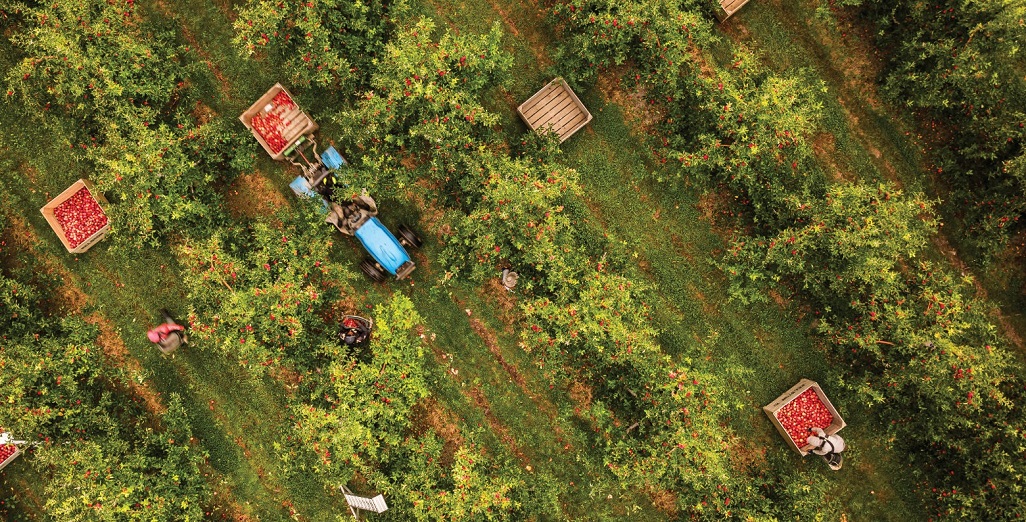